The cement industry is witnessing a major breakthrough in kiln electrification technology, with the ELECTRA project and initiatives from SaltX and Coolbrook offering viable solutions for CO₂ emissions reduction.
ELECTRA Project: Plasma-Based Cement Kiln Technology
Heidelberg Materials has announced that the ELECTRA project, funded by the European Union, has successfully tested the first plasma-based cement kiln in Sweden. This technology enables clinker production without fossil fuels, effectively eliminating CO₂ emissions and simplifying the carbon capture process.
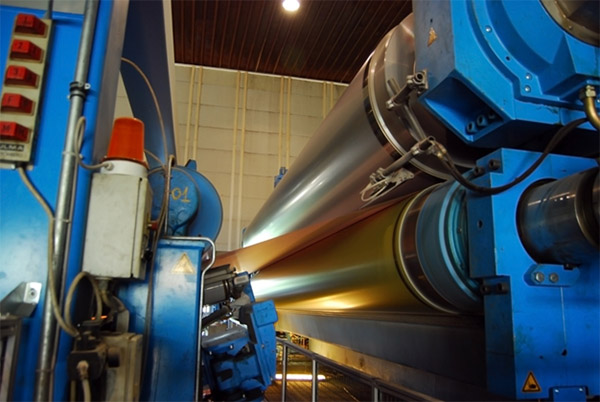
The ELECTRA project is developing electric-powered kilns for cement, lime, and slaked lime production, capable of reaching 2,000°C. With high flexibility, the system can operate in various hybrid modes, reducing initial investment costs. Launched in Jyväskylä, Finland, in 2024, the project aims to cut CO₂ emissions by 90% in cement production.
SaltX Partners with Thyssenkrupp Polysius
SaltX has signed a letter of intent with Thyssenkrupp Polysius to develop the next generation of fully electrified cement plants. The Electric Arc Calciner (EAC) technology from SaltX will be integrated into Thyssenkrupp Polysius’s green system solutions.
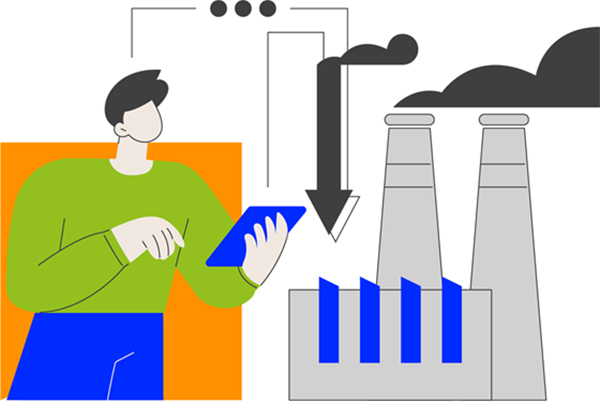
This technology is also being applied in the steel industry with SMA Mineral, where it has produced high-quality quicklime at a Hofors test facility. In February 2025, SaltX reported a 99% calcination rate in specific trials. The SaltX pilot plant, with a capacity of 8MW, will produce 120 tons of quicklime per day in Norway, with plans to scale up to 100MW and 1,500 tons per day by 2030.
Coolbrook’s Ambitious Expansion Plans
Coolbrook, a Finnish startup, is collaborating with JSW Group in India to test its RotoDynamic Heater™ technology, which can reduce CO₂ emissions by 30% in heavy industries and achieve 1,700°C temperatures without fossil fuels.
Ambuja Cements has signed a strategic partnership with Coolbrook to scale up the technology. The RotoDynamic Heater™ can be applied in clay calcination, clinker preheating, and white cement production, reducing fossil fuel use by 50% while increasing production capacity by 25%.
The Race to Electrify the Cement Industry
Which technology will become the industry standard remains uncertain, as companies require sufficient funding and strategic partners to bring these innovations to commercial scale. However, with strong investments in green technology, electrification is emerging as a key driver in reducing CO₂ emissions and leading the cement industry toward a more sustainable future.
Source: ximang.vn